Routine maintenance is the backbone of any reliable manufacturing operation. It keeps machines running smoothly, prevents costly breakdowns, and creates a safer environment for everyone on the floor. When done right, it saves time, money, and a whole lot of headaches.
But let’s be real — routine maintenance isn’t always as “routine” as it sounds. Teams have to find their way around busy production schedules, track down parts or tools, and often work with paper forms or outdated systems. Things slip through the cracks, work piles up, and before you know it, you’re dealing with unplanned downtime that could’ve been avoided.
In this article, we’ll break down the typical routine maintenance workflow, the different ways it can be scheduled, and most importantly — how you can make routine work more efficient and less disruptive on your production floor.
What is routine maintenance?
Routine maintenance is the regular, planned upkeep of equipment and systems to keep everything running smoothly. It’s the day-to-day stuff — minor but important tasks that are usually classified as preventive work.
The typical routine maintenance workflow looks something like this:
- A task is scheduled based on time, usage, or condition.
- A technician completes the task — like checking fluid levels, tightening bolts, or cleaning filters.
- The work is logged (ideally in a digital system).
- The task is rescheduled for its next cycle.
These tasks don’t take long individually but add up fast — especially if you manage dozens or hundreds of assets. Done consistently, routine maintenance helps catch issues early and avoids bigger, more expensive problems down the line.
Here are a few examples of routine maintenance work across different industries:
- Manufacturing: Lubricating machine parts, inspecting safety guards and emergency stops, replacing worn belts or filters.
- Construction: Checking tire pressure and fluid levels on heavy equipment, inspecting scaffolding and safety harnesses, and cleaning generator air filters.
- Healthcare: Sterilizing equipment after each use, calibrating diagnostic machines, and inspecting HVAC and air filtration systems.
- Fleet management: Oil changes after a set number of miles, tire rotations, brake pad checks, and inspections of lights, signals, and wipers.
- Property maintenance: Testing smoke detectors and emergency lighting, cleaning gutters and checking roofs, and servicing HVAC systems before peak usage.
Types of routine maintenance
There is no official categorization for routine maintenance. However, we can discuss how routine tasks are typically scheduled.
1. TIME-BASED MAINTENANCE (TBM)
- What it is: Performed at regular, scheduled intervals (daily, weekly, monthly, etc.).
- Examples: Lubricating bearings every week, replacing filters monthly.
- Goal: Prevent wear and tear, regardless of current equipment condition.
2. USAGE-BASED MAINTENANCE
- What it is: Triggered by specific usage metrics like operating hours, cycles, or mileage.
- Examples: Changing oil after 500 hours of operation, inspecting belts after 1,000 cycles.
- Goal: Align maintenance with actual wear patterns rather than time.
3. CONDITION-BASED MAINTENANCE (CBM)
- What it is: Performed when certain indicators show signs of equipment deterioration.
- Examples: Replacing a part when vibration levels exceed a set threshold.
- Goal: Use real-time data (via sensors or manual checks) to service equipment based on its current condition.
Routine maintenance represents proactive work. As such, it is an integral part of any proactive maintenance strategy.
How to make routine maintenance more efficient and less disruptive
Routine maintenance is essential — but it shouldn’t feel like it is getting in the way of your manufacturing operations. The key is to build a system that keeps everything flowing without pulling teams away from production or chasing down missing parts.
This section covers five practical ways to simplify your routine maintenance process and make life easier for your maintenance crew.
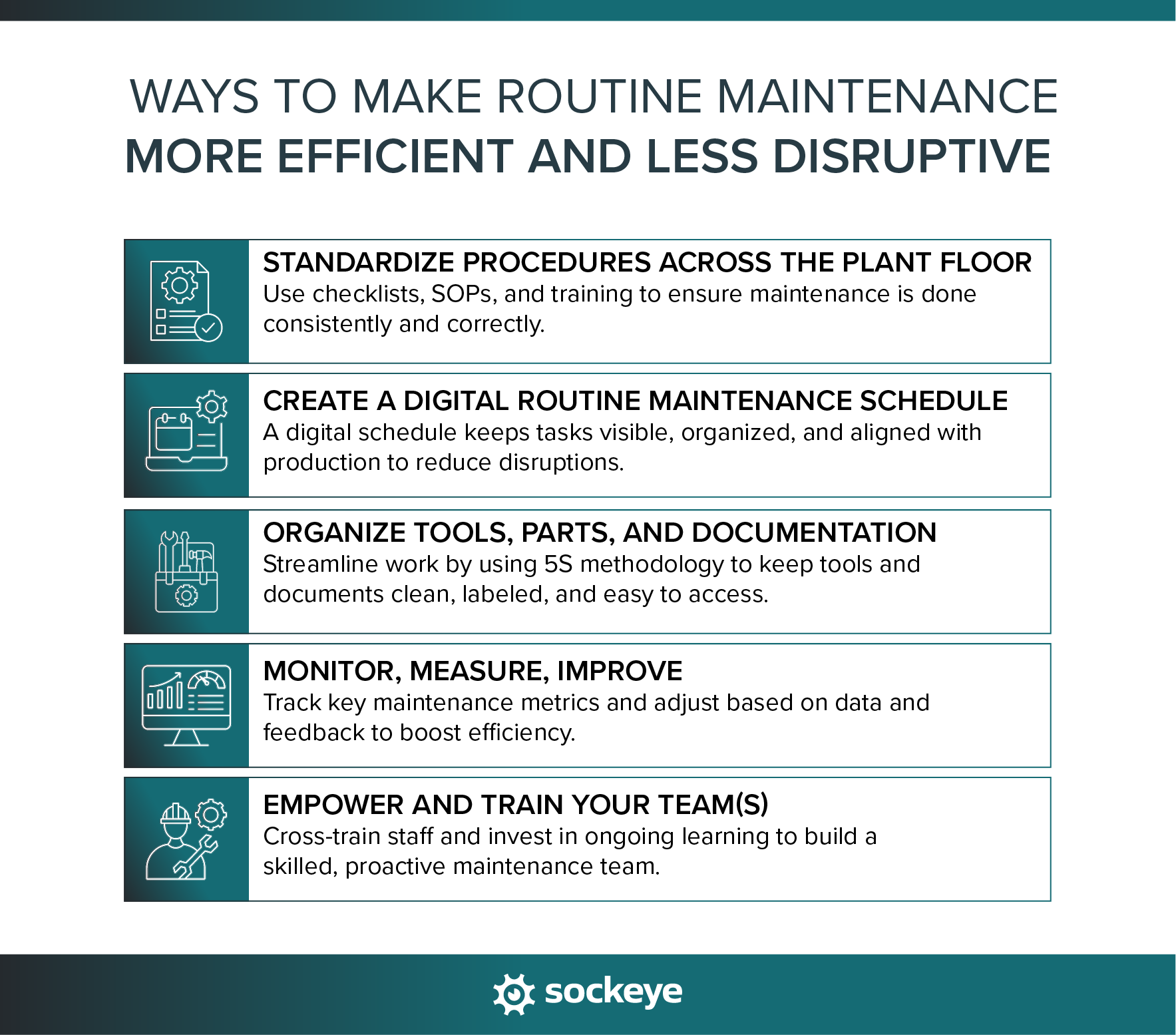
1) Standardize procedures across the plant floor
Inconsistent maintenance lowers equipment reliability. One tech might do a thorough check, while another misses a key step — not because they’re careless, but because there’s no clear standard.
Maintenance checklists help ensure that simple tasks are done correctly every time. Whether it’s greasing a motor or inspecting safety systems, checklists keep everyone aligned.
You can go a step further and write up Standard Operating Procedures (SOPs) for recurring maintenance work. Task an experienced technician to outline what needs to be done, how to do it, and what tools or parts are required. As a nice bonus, this will also simplify maintenance planning.
Lastly, invest in training. Even the best procedures won’t help if people have issues following them. A well-trained team that understands the “why” behind routine maintenance will spot issues faster, take more ownership of their work, and help build a culture of reliability.
2) Create a digital routine maintenance schedule
Planning is half the battle when it comes to routine maintenance. Without a clear schedule, tasks will get missed, and crews will get overbooked.
Switching to a digital maintenance schedule makes planning, assigning, and tracking routine tasks easier. It gives your team visibility into what needs to be done, when, and by whom. Preventive maintenance scheduling software like Sockeye helps maintenance teams build schedules that are easy to update and balance across crews.
A good routine maintenance schedule also works with production — not against it. Coordinate with production managers to slot in maintenance tasks during slower periods or planned downtime. If work needs to shift because of delays or changes on the production floor, a digital system like Sockeye enables you to just drag and drop work to the next available slot.
When you have a live, verified schedule visible to all teams, routine maintenance becomes much more manageable — and less disruptive.
3) Organize tools, parts, and documentation
Have you ever lost 20 minutes searching for the right wrench or the right manual? Disorganization is one of the biggest time-wasters in maintenance.
Start by setting up a clean, labeled, and accessible storage area for your tools and spare parts. This will reduce wasted time and help prevent mistakes, like grabbing the wrong part or a malfunctioning tool.
Implementing the 5S methodology can significantly improve how your maintenance team organizes tools, parts, and workspaces. Here’s what it looks like in action:
- Sort: Remove unnecessary tools, parts, and junk from the workspace. Only keep what’s actually needed. This reduces clutter.
- Set in Order: Arrange tools and parts so they’re easy to access and return. Use labels, tool shadow boards, or color-coding. The goal is to make it obvious where everything goes.
- Shine: Clean the workspace and equipment regularly. This isn’t just about appearance — clean areas are easier to work in and help spot issues like leaks or wear early.
- Standardize: Create standard procedures for organizing, cleaning, picking up and returning items to inventory, and similar.
- Sustain: Make it a habit. Train the team and do an occasional audit to reinforce the importance of staying organized. This step ensures 5S doesn’t fade over time.
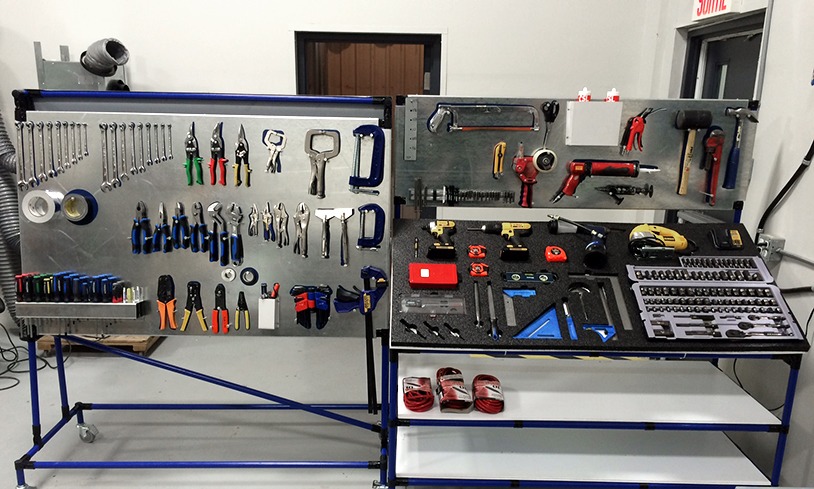
Lastly, don’t forget about your documentation. Keep equipment manuals, past work orders, and checklists organized and easy to find — preferably in a digital form inside a CMMS or EAM software. When your techs can pull up everything they need on a tablet or phone, they’ll spend less time searching and more time doing.
4) Monitor, measure, improve
You can’t improve what you don’t track. To make routine maintenance truly efficient, you need to keep an eye on how well your current processes are working — and adjust when they’re not.
Start by tracking key metrics like:
- MTTR (Mean Time to Repair): How long it takes to complete a repair once it starts.
- MTBF (Mean Time Between Failures): How long equipment typically runs before it breaks down.
- Schedule Compliance: The percentage of scheduled tasks completed on time.
- Preventive vs. Reactive Hours: How much time your team spends on planned work vs. emergency fixes.
These numbers give you a clear picture of where your maintenance program stands and where the bottlenecks are.
Every so often, conduct an audit or a quick review of your routine tasks. Are checklists being followed? Do certain pieces of equipment need more or less attention? Are the parts/time spent on routine maintenance accurately logged? Use the data and technician feedback to make smart adjustments.
Routine maintenance schedules don’t need to change often, but shouldn’t be set in stone either. By measuring what matters and making small, informed changes, you’ll keep getting better — and so will your equipment uptime.
5) Empower and train your team(s)
One surefire way to boost efficiency is through cross-training. Teaching some of your machine operators how to handle routine tasks — like lubrication, visual inspections, or minor adjustments — frees up your maintenance techs to focus on more technical work. It also creates more eyes on the floor to catch issues early.
As noted by Michael Blanchard at Plant Services:
“Operators need to be trained to clean and inspect equipment and perform basic maintenance tasks such as tightening fasteners. They also need to know when to reach out for help should the task appear beyond their capabilities.”
Another thing that facilities need to do is actively encourage technician feedback. They’re the ones doing the work day in and day out, and they’ll often have ideas on how to streamline tasks, improve checklists, or fix recurring problems. Try to create a culture where their input is heard and acted on.
Finally, don’t push ongoing training aside. Whether it’s brushing up on safety procedures, learning how to use new tools, or understanding maintenance software, keeping your team sharp ensures routine tasks are completed faster and with fewer mistakes.
Research shows that training improves maintenance performance. Empowered teams are more engaged, more consistent, and more likely to take ownership of their work — exactly what you want for a solid maintenance program.
How Sockeye helps streamline routine maintenance
Sockeye is a CMMS bolt-on designed to simplify maintenance scheduling — be that reactive or routine work. It gives maintenance teams a clear overview of what’s due, what’s coming up, and how work is distributed across crews.
With Sockeye, you can:
- Build weekly maintenance schedules with just a couple of clicks
- Use drag-and-drop to reschedule work quickly
- Provide a live, verified schedule that keeps everyone on the same page
- Easily level workload between different crews
- Track task completion, backlog, delay reasons, and team workload in real-time
- Get instant visual reports on key scheduling metrics
By replacing whiteboards, spreadsheets, or clunky legacy systems, Sockeye helps maintenance teams get more done with less stress. Take the guesswork out of routine maintenance so your team can stay focused and organized.