Plant maintenance is more complex than ever. As equipment grows more advanced and production schedules get tighter, plant managers are under pressure to keep things running smoothly with fewer resources, leaner teams, and shrinking margins for error.
If you decide to stick around, we will give you strategies, tips, and tools to streamline maintenance on your plant floor.
What is plant maintenance?
Plant maintenance is everything you do to keep equipment, machines, and facilities running safely and reliably. That includes routine inspections, emergency repairs, preventive maintenance, and everything in between.
Why does it matter? Because when machines go down unexpectedly, everything stops — and that downtime is expensive. Good maintenance keeps production on track, protects your assets, and helps you get more out of your labor and budget.
Here are some of the biggest challenges plant maintenance teams are up against:
- High cost of unplanned downtime: Equipment failures often mean halted production, lost revenue, and costly catch-up work. One hour of downtime costs between $39,000 and $2 million, depending on the industry.
- Difficulty in scheduling preventive maintenance: It’s tough to plan around production schedules, labor availability, and shifting priorities.
- Labor shortages and overloaded teams: With fewer skilled technicians available, maintenance teams are stretched thin and constantly fighting increasing backlogs.
- Over-reliance on reactive maintenance: Waiting for things to break creates chaos. A proactive approach is more efficient, but harder to implement without the right systems in place.
- Trying to manage everything manually or with outdated systems: Spreadsheets and paper don’t scale. As complexity grows, it’s easy for things to slip through the cracks.
Tackling these challenges starts with choosing the right maintenance strategy — one that fits your assets, your team, and your goals.
Choosing the right plant maintenance strategy
There’s no one-size-fits-all approach to plant maintenance. The best strategy is usually a mix — combining run-to-failure, preventive, condition-based, and predictive maintenance, depending on the type of equipment you run, its criticality, and the available internal resources.
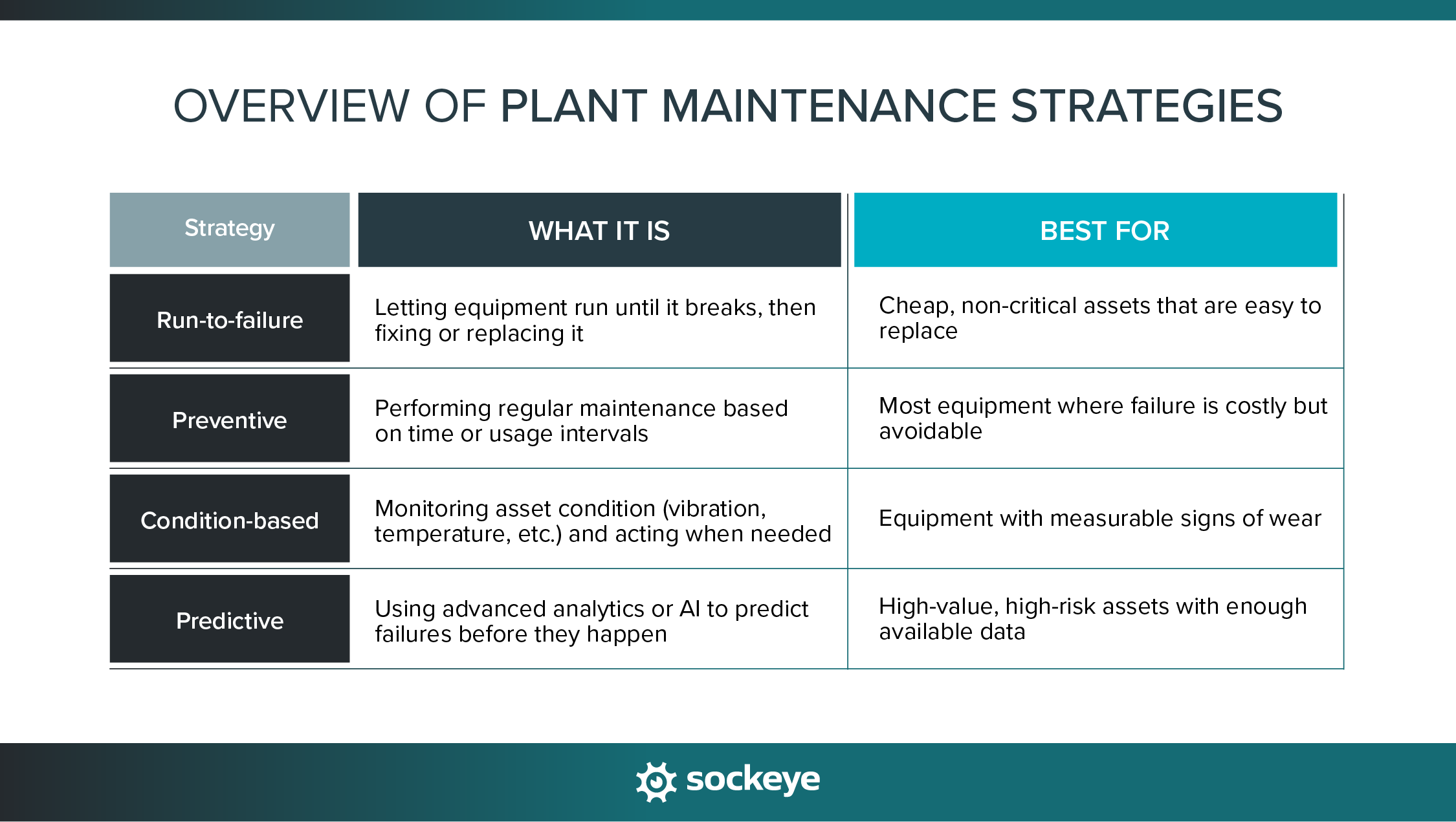
The key is to apply the right strategy to the right asset. For example, you might use:
- Run-to-failure for inexpensive, non-repairable assets, such as fans and light bulbs, which are easily replaced once they stop working.
- Preventive maintenance for pumps and motors that need regular lubrication.
- Condition-based or predictive maintenance for production-critical machines like CNC machines, high-speed packaging lines, or industrial compressors — where an unexpected failure would halt operations or require costly repairs.
Choosing the right mix helps you optimize your team’s time, budget, and schedule.
Tools you need in your corner
Even with a good strategy in place, maintenance teams need the right tools to execute. Paper, spreadsheets, and tribal knowledge might work for a while, but they don’t scale — and they definitely don’t make life easier when production picks up the pace.
Modern plant maintenance relies on two core tools:
- A software system to manage work, assets, and parts.
- A flexible way to schedule and (re)assign maintenance work in real time.
Let’s break those down.
Plant maintenance software (CMMS or EAM)
Most plants today (approximately 70%) use either a CMMS (Computerized Maintenance Management System) or an EAM (Enterprise Asset Management) platform.
Here’s why modern maintenance software makes a difference:
- Asset management: Keep detailed records of every piece of equipment — from manuals and specs to service history and performance data.
- Spare parts inventory tracking: Know what’s in stock, where it is, and when you’re running low — so you’re not caught off guard during a repair.
- Work order tracking: Create, assign, and monitor work orders from start to finish. Get visibility into what’s planned, what’s in progress, and what’s overdue.
- Reporting & insights: Turn data into action. Spot trends, identify recurring issues, and justify budget or staffing changes with real numbers.
These tools give you the foundation to move away from reactive maintenance and take control of your plant maintenance processes — but they’re only part of the equation. Scheduling is where things often break down.
Maintenance scheduling add-on
Scheduling is at the core of every maintenance process. When it’s done poorly, it underuses or overworks technicians, and preventive tasks get skipped. All you get is more downtime and higher maintenance costs.
Even with a solid CMMS or EAM in place, maintenance scheduling can still be a major headache. Why? Because their built-in scheduling tools are either too rigid or too hard to use.
As many facilities combine planner and scheduler into a single role, that person ends up battling the scheduling tool most of their shift. They have little to no time to plan jobs properly. Tools like Sockeye help turn the script. Work can be scheduled quickly, leaving more time for proper maintenance planning.
Replacing a CMMS that is performing well in other areas to solve scheduling is overkill — it’s throwing the baby out with the bathwater. Instead of replacing your CMMS or EAM, consider using our simple maintenance scheduler. It’s a lightweight but powerful tool built specifically to simplify scheduling for busy plant maintenance teams.
Here’s what it brings to the table:
- Drag-and-drop scheduling: Quickly assign and adjust tasks with a visual interface and powerful scheduling automation.
- Real-time labor availability: Easily track who’s available, who’s booked, and who’s off — so you can assign work efficiently.
- Schedule visibility: Sockeye always displays the latest schedule, making it easy to track work in progress, what was missed and why, and what’s coming up next week. Teams can coordinate to ensure assets are available for PMs while minimizing production disruptions.
- Automated reporting: Eliminate manual updates and get instant visibility into your schedule effectiveness and team performance.
Fits into your existing workflow: Sockeye integrates with your current CMMS or EAM — so you don’t have to rip and replace anything. It just makes your current system smarter and easier to use.
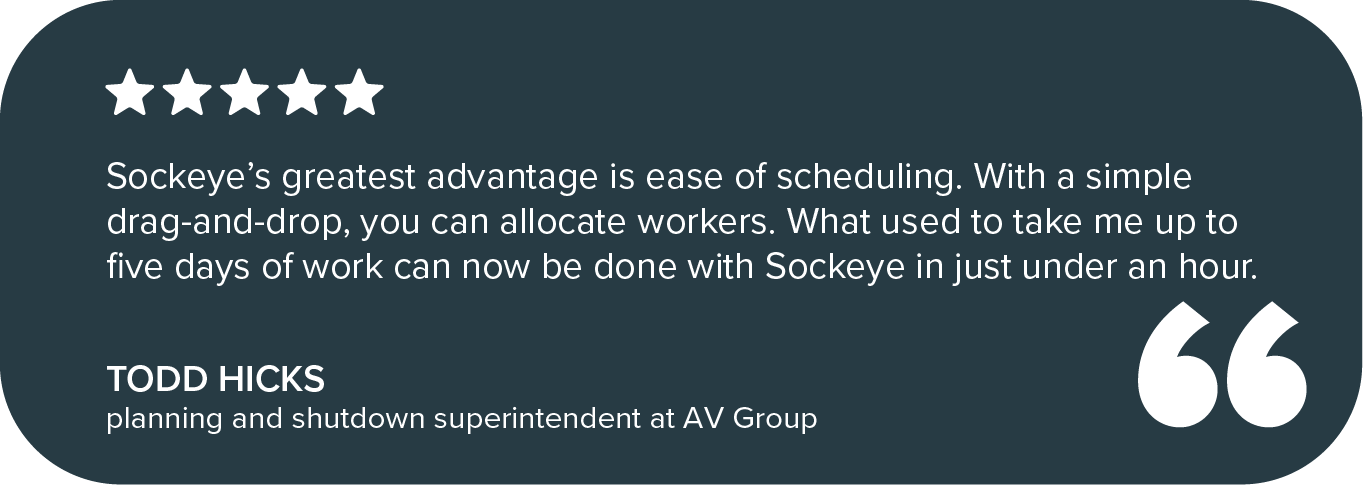
With a better scheduling tool, you’re not just making life easier for planners — you’re improving technician productivity, reducing delays, and getting more out of your existing CMMS/EAM investment.
Tips for getting the most out of your plant maintenance efforts
To really move the needle, you also need to build smart habits into your day-to-day operations. Below are a few practical ways to boost the impact of your maintenance efforts — without adding more chaos or administrative work.
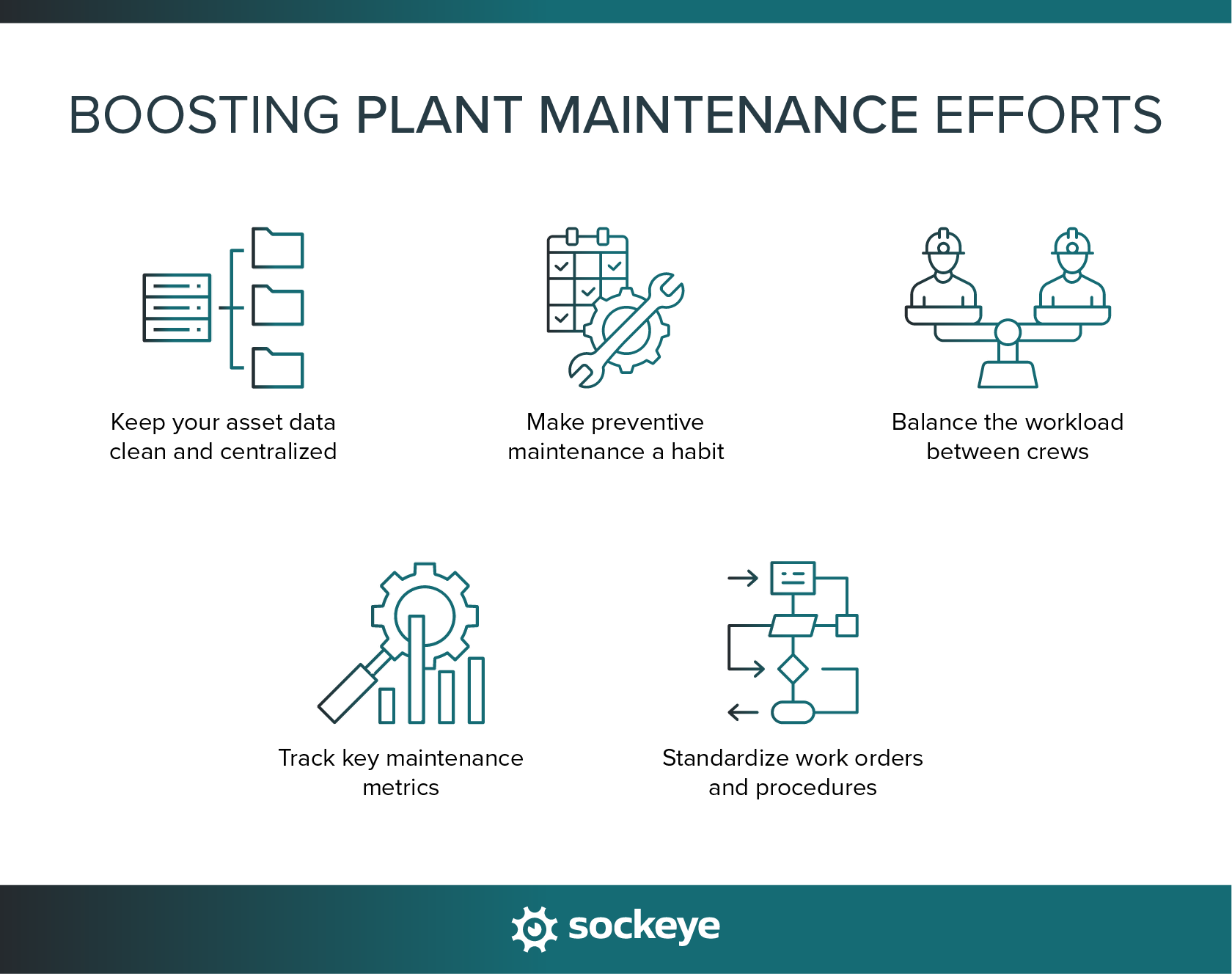
1. Keep your asset data clean and centralized
If your asset information is scattered across binders, spreadsheets, filing cabinets, or people’s heads, that is a recipe for disaster.
Ensure every important asset has a digital record that includes:
- Manuals and specs
- Service history
- Warranty information
- Known issues or recurring problems
A CMMS is a great way to centralize all of that data. Planners and schedulers can use it to make better job plans and create more effective PM schedules. All of which leads to fewer mistakes, delays, and wasted trips.
2. Make preventive maintenance a habit
Having a preventive maintenance plan is one of the most effective ways to avoid unexpected breakdowns — but it’s not always easy to follow through.
In a busy manufacturing plant, PM often takes a backseat to urgent repairs, especially when resources are tight or schedules are unclear. But skipping routine maintenance only increases the risk of future problems.
To build a stronger, more proactive maintenance culture:
- Start small and stay realistic. Focus on critical assets and build up over time.
- Check labor availability before committing to PM schedules — don’t just assume time will magically appear.
- Use SOPs and checklists to make sure tasks are completed correctly and consistently.
- Automate maintenance scheduling to give your planners more time to focus on creating clear, accurate, and realistic job plans.
The more consistent you are, the fewer surprises you’ll face — and the easier it becomes to stay proactive.
3. Balance the workload between crews
It’s easy for work to pile up on your most experienced techs or specific shifts — especially when you’re assigning work orders manually or juggling last-minute changes.
An unbalanced workload leads to burnout, missed PMs, and longer response times.
Your scheduling tool should help fix this by providing a clear view of:
- Who’s available
- What skills do they have
- How much work is already on their plate
That visibility helps you level work between crews — which is something Sockeye makes super easy.
With the right information at their fingertips, schedulers will have an easier time prioritizing and assigning work based on skills, availability, and urgency. This not only improves morale, but it also boosts productivity across the board.
4. Track key maintenance metrics
Tracking even a few basic maintenance KPIs provides the insight you need to identify issues early, optimize your plant maintenance processes, or make a stronger case when requesting additional resources.
You can start with a few meaningful metrics:
- Schedule compliance: Are tasks getting done when they’re supposed to?
- Mean time between failures (MTBF): How long does equipment run before needing repairs?
- Planned vs. unplanned work ratio: Are you staying proactive, or just reacting?
- Work order backlog: How much work is piling up, and how fast are you closing it?
Use your CMMS or scheduling tool’s reporting features to track these over time.
5. Standardize work orders and procedures
When every technician does the same job a different way, quality suffers — and so does efficiency. Standardizing how common tasks are documented and executed makes a big difference.
Start by creating templates for recurring work orders, including:
- Step-by-step instructions (including annotated images and even videos if needed)
- Required tools and parts
- Safety checks
- Estimated time to complete.
Standardized work orders reduce guesswork, shorten training time for new hires, and ensure consistent results — no matter who’s assigned to the job.
It’s one of the simplest ways to boost quality, speed, and accountability all at once.
Measure twice, cut once
Plant maintenance shouldn’t feel like a constant scramble. With the right strategy and tools in place, you can outrun the chaos.
Start by figuring out where you are today:
- Are you relying too much on reactive fixes?
- Is scheduling a constant bottleneck?
- Are you using the right tools to support your team?
Small changes — like improving how you schedule or cleaning up asset data — can have a big impact.
If your team struggles to consistently create schedules or stick to them, consider implementing Sockeye as your manufacturing maintenance scheduling software.
We offer a 30-day free trial that doesn’t require involvement from your IT department. Get a proof of concept and user adoption before spending a single cent.
Looking for scheduling tips and solutions for a specific type of production plant? Check out the following resources: