When it comes to keeping a maintenance team running smoothly, few things are as important as effective scheduling. Get it wrong, and you’re looking at chaos, frustrated crews, and missed work piling up fast.
That’s where CMMS (Computerized Maintenance Management Systems) come in. They promise to organize everything — from your work orders and assets to maintenance history. And many CMMS platforms do a decent job at that.
But here’s the thing: most of them fall short when it comes to scheduling. In fact, they can be so clunky or complicated that many teams revert to using Excel to schedule work. We have seen it many times.
In this article, we’ll dive into the common issues that make CMMS scheduling a pain, why teams struggle to make it work, and how Sockeye is stepping in to solve these problems.
Common issues with scheduling maintenance work with a CMMS
Before we get into it, quick note: we’re from Sockeye, and yes — we build maintenance scheduling software. But our solution doesn’t replace a CMMS; it bolts onto it to simplify how you schedule and track maintenance work.
There are tons of CMMS solutions out there — from old-school legacy systems to modern, cloud-based platforms. Some are packed with features, others are more bare-bones. To be clear, we’re not calling out any specific product here. We are discussing the average experience that CMMS users have with scheduling.
Without further ado, here are the most common complaints we hear from maintenance planners and schedulers.
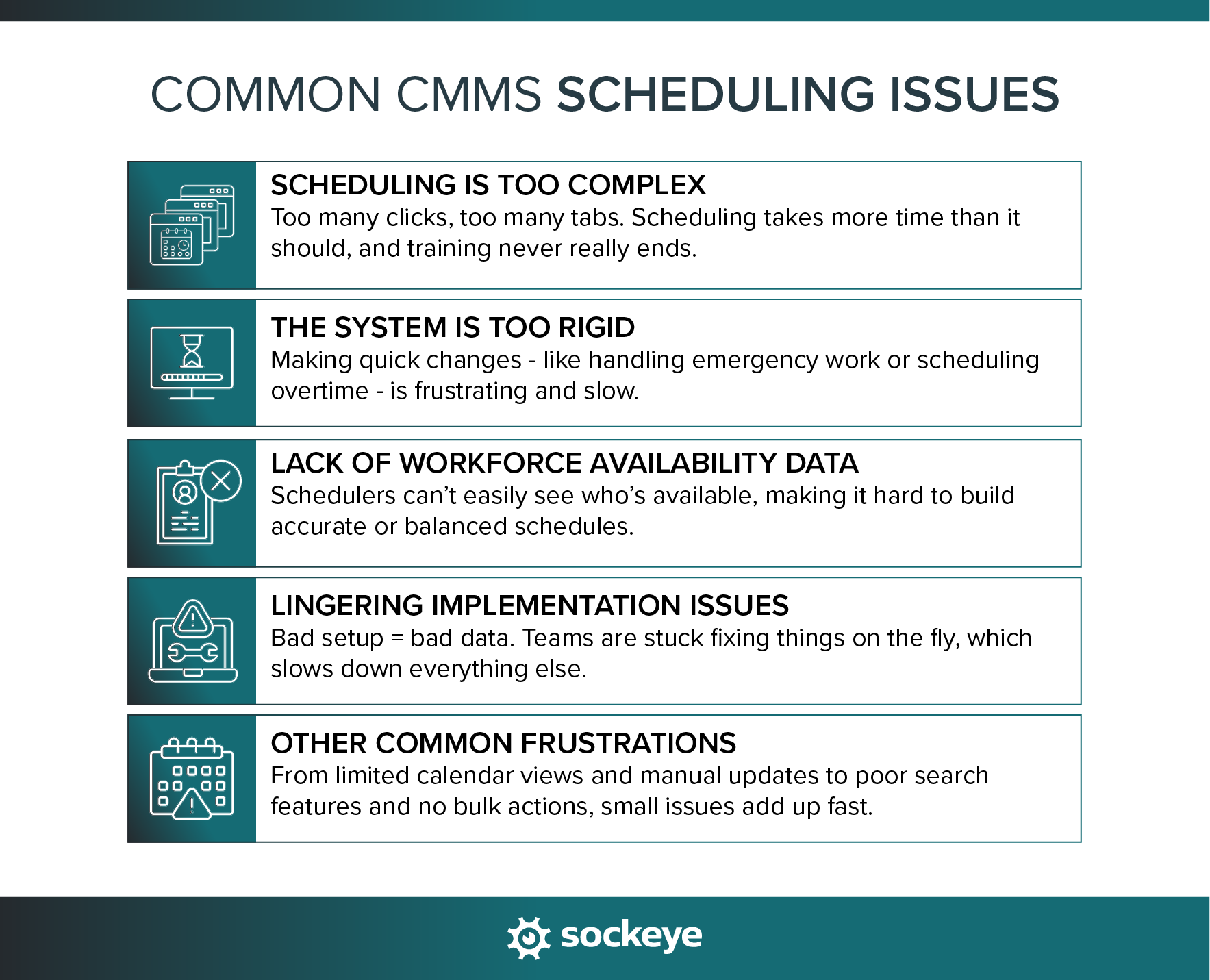
Scheduling is too complex
You’d think putting a work order on a calendar would be simple. But for many users, it becomes a clickfest. You have to bounce between multiple tabs just to get the info you need — technician availability here, work order details over there, priorities in another spot, etc. It’s a mess.
To make things worse, some teams never receive proper training in the first place, and even those that do still find themselves needing ongoing support because the system is so unintuitive.
We’ve heard from more than a few schedulers who were basically self-taught — and not by choice.
The system is too rigid
Another common gripe? CMMS platforms can be way too inflexible.
Maintenance schedules don’t live in a perfect world. Things come up — emergency work, last-minute changes, people calling in sick. But when your CMMS makes it a pain to adjust the schedule, you’re stuck wasting time on something that should be quick.
We’ve heard stories like this more than once: a scheduler needs to assign overtime work, but their CMMS won’t allow it unless they manually adjust the worker’s available hours first. Now you have to jump through hoops to schedule a simple task.
A lot of these systems were built with rules that don’t match the reality of a busy maintenance team. And when your tool doesn’t flex with your workflow, it stops being useful.
Lack of workforce availability data
In many CMMS platforms, workforce availability data is either missing or outdated. That makes it tough to schedule effectively — because how can you plan the week when you don’t know who’s on shift, who’s off, or who’s already fully booked?
This leads to a lot of guesswork. You end up building a schedule based on what should be possible, only to have to rework it later when the real picture comes into focus. This is detrimental to maintenance productivity.
When labor availability isn’t part of the equation, it’s impossible to level workloads between teams and individuals, avoid conflicts, or make smart trade-offs. It’s like trying to play Tetris with missing pieces.
Lingering implementation issues
Here is another issue we hear often: the implementation didn’t go smoothly, and now our team is stuck with bad or incomplete data.
Maybe not all the assets were uploaded, maybe the labor data is missing, maybe the work order info is incomplete or duplicated. Whatever it is, it’s messing with their ability to schedule properly.
Fixing it is a whole other challenge. Nobody has extra hands sitting around to clean up a messy implementation. So the fixes get done ad hoc, if they get done at all. And until that happens, the scheduling features are basically unusable.
It’s frustrating because the team wants to use the system, but they keep running into roadblocks left over from day one.
Other CMMS scheduling issues you might encounter
There are a bunch of additional, smaller issues that pop up when teams try to schedule with a CMMS.
These might not be dealbreakers on their own, but together, they make the whole process slower and more painful than it should be:
- Too many clicks, not enough time. Scheduling or building reports takes way longer than it should.
- Spreadsheet juggling. Many schedulers plan in Excel and then go back to the CMMS to update everything manually.
- Lack of visibility. It’s hard to tell what work is done and what’s still open, which makes prioritizing for the next week tricky.
- Poor schedule visualization. It’s hard to visualize the weekly schedule, especially in legacy or older maintenance systems.
- Can’t search or filter easily. Want to find a specific work order in your backlog? Good luck. You’ve got to follow a procedure just to run a search.
- Limited team access. Not everyone can see the schedule or the latest updates, which leads to confusion and miscommunication.
- No bulk assignment. Some systems force you to assign work orders one at a time — which, again, is a major time waster.
- Missing work order hierarchy. You can’t easily view the breakdown of related or sequential tasks under a main work order, which makes planning more difficult.
Over time, these issues add up and push teams away from using the CMMS. Instead, they create workarounds that aren’t ideal — but at least they work for them.
Sockeye solves all of the issues with your CMMS schedule
Okay, so we’ve gone through the laundry list of ways CMMS scheduling can fall short. But here’s the good news: it doesn’t have to be that way.
Sockeye is explicitly built to take the pain out of scheduling. It doesn’t replace your CMMS — it works with it. Thanks to two-way integration, all your existing data — work orders, history, asset records — stays right where it is. Sockeye just gives you an easier and faster way to create daily and weekly schedules.
Let’s quickly walk through how it works.
Focus on simplicity
Everything about Sockeye is built to be simple:
- Implementation: You don’t need a dedicated IT team or months of onboarding. Just plug in your schedule and shift patterns, and you’re off to the races.
- Training: Most teams are up and running after a single 1-hour session. It’s that easy to use.
- Scheduling work: You can schedule tasks in bulk with just a couple of clicks using our built-in maintenance scheduling automation.
- Rescheduling work: Work can be rescheduled by simply dragging and dropping work to the next available slot.
- Reporting: Reports are built automatically and presented using graphs and other visual aids. Sockeye tracks dozens of scheduling KPIs out of the box, but you can also add custom KPIs. Plus, we have BI integration that offers even more granular insights and additional ways to visualize the data.
Real-time availability data
One of Sockeye’s biggest strengths? You can see who’s available to do the work — right now.Sockeye pulls in real-time data on technician and contractor availability, either directly from your HR or workforce software or by inputting your shift patterns. That means when you’re building a schedule, you’re working with the actual picture of who’s on shift, who’s off, and who’s already booked.
This visibility is a game-changer. It lets schedulers avoid overtime by balancing workloads between crews. Plus, it avoids the kind of last-minute reshuffling that drives everyone nuts.
Powerful scheduling automation
When you have a large backlog, manual scheduling is a huge time sink.
Sockeye makes it easy to schedule work orders in bulk. Just:
- Select the crew and week you’re scheduling for
- Use our search functionality to quickly find the work you want to schedule
- Select the work orders and click on the “Schedule” button — our maintenance scheduling automation will check who is available and assign and schedule work accordingly.
Here’s a short video that shows this automation in action:
The result? A live, visual schedule that keeps your whole team on the same page, always reflecting the latest updates.
Workflow built by maintenance schedulers
We worked closely with experienced maintenance schedulers from day one to ensure the workflow accurately reflects how scheduling works on a busy plant floor.
In a manufacturing environment, schedules change all the time. Equipment breaks down. Priorities shift. People call in sick. That’s why Sockeye makes it super easy to reschedule work on the fly — whether you’re moving a job to a different day or reassigning it to another crew. It takes seconds, not hours.
It’s fast, flexible, and built for real-life workloads.
Try Sockeye today – no strings attached!
If you’re not satisfied with how your CMMS handles scheduling, Sockeye is precisely what you need.
And the best part? You can try it out for free — so you can make sure it works for you before spending a single cent.
All we need to get you started is your current schedule, your shift patterns, and just one hour of your scheduler’s time. That’s it. You won’t need help from IT or a big internal project.
Book a quick demo with our team and let us show you how much easier scheduling can be!