DAIRY PLANT MAINTENANCE SCHEDULING SOFTWARE
Simplify Scheduling and Boost Reliability at Your Dairy Plant
Stick to preventive weekly schedules that support strict hygiene standards and keep production running smoothly. Use Sockeye to automate weekly scheduling, increase labor utilization, and prevent equipment issues.
Used by forward-looking dairy plants
We built a maintenance scheduling tool so intuitive and effective, it takes just one hour to learn — and 98% of breweries who try it dairy plants that try it stick with it for the long haul.
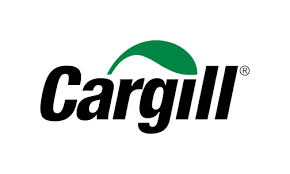
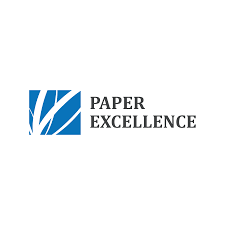
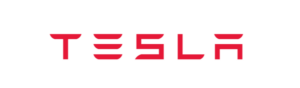
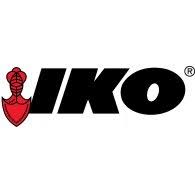
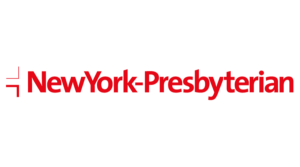
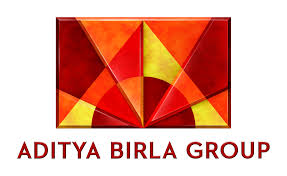
Here’s how Sockeye works
KEY FEATURES
Automatic scheduling
Schedule visualization
Work order status tracking
Delay reasons tracking
SMRP and custom KPI reports
Full CMMS/HR system integration
Perfect for
Plant that have a CMMS or EAM
Sockeye works best as a CMMS add-on. If your team struggles to schedule work through existing software, use Sockeye’s intuitive interface instead.
Teams that need to get more work done
Complicated scheduling kills productivity. Our automation and availability data help you schedule more work by balancing workload between crews.
Simpler & more efficient scheduling
Sockeye is a purpose-built scheduler that’s easy to roll out and effortless to use. It’s 100% focused on scheduling — and it’s udderly good at it.
Test Sockeye for 30 days.
No IT involvement required.
Confirm user adoption and get a proof of concept before spending a single cent.
TAKE THE FREE TRIALPM SCHEDULING
Automate maintenance (re)scheduling
Sockeye makes it easy to assign PMs for routine maintenance and cleaning tasks, balance workloads across shifts, and ensure nothing gets missed — helping your team maintain compliance and keep production running smoothly.
Share live schedules to keep your frontline teams aligned and accountable. Easily reschedule work by dragging and dropping tasks to the next available slot.
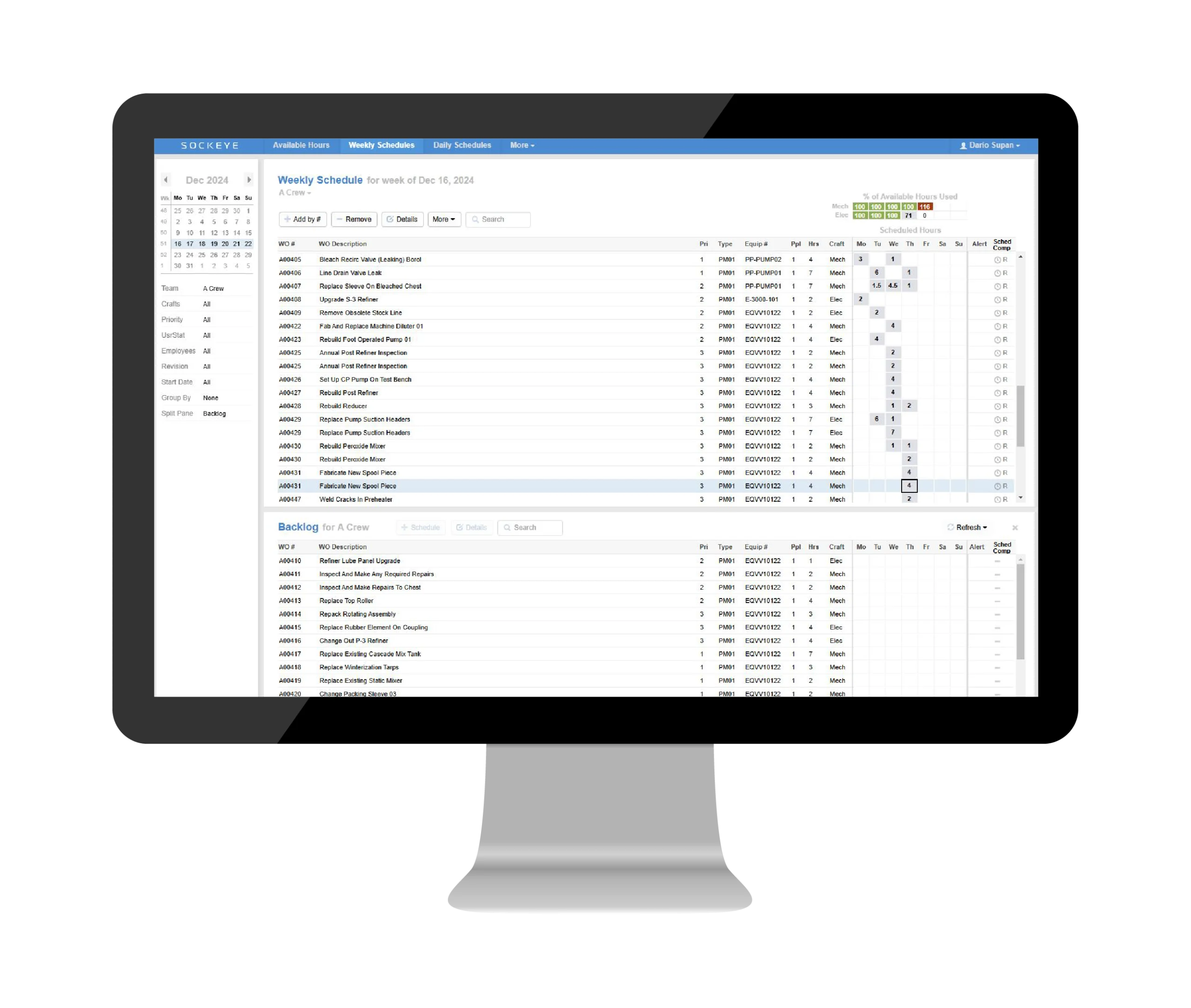
LABOR AVAILABILITY
Do more with fewer resources
Sockeye gives you real-time visibility into crew and contractor availability. You can easily level work across teams and maximize labor utilization without resorting to overtime.
“Sockeye identifies where deficiencies are in your man hours. For instance, if Crew A is 40 hours over schedule, but Crew B is only 35% scheduled, you can move your resources to level it out to avoid overtime pay. That saves you money.”
Todd Hicks, Planning and Shutdown Superintendent at the AV Group
EQUIPMENT RELIABILITY
Improve reliability, reduce downtime
From pumps and homogenizers to pasteurizers and separators, Sockeye helps you keep critical dairy processing equipment running by making preventive maintenance easier to schedule and manage.
Track delay reasons for PMs and WOs, free up time to prepare jobs properly, and keep your most critical assets operating at peak reliability.
KPI REPORTING
Track and report relevant KPIs
Automatically generate SMRP and custom KPI reports to track schedule compliance, labor utilization, reactive vs preventive ratios, and backlog trends — then freely send that data to your BI tool.
Track how specific work orders impact reliability and see how effective your current maintenance schedule truly is.
REGULATORY COMPLIANCE
Stay compliant with dairy industry regulations
From FDA regulations to pasteurization and sanitation standards, dairy compliance depends on timely, well-documented maintenance. Sockeye creates a digital audit trail, so you’re always ready for inspections and confident in your compliance.
Build schedules your team can adhere to, and always know what’s been done, what’s in progress, and what’s due next — all in one place.
Schedule more work.
Get more work done.
Let us help you create a highly productive maintenance team.
Book a DemoDairy plant maintenance best practices
Maintaining equipment in a dairy plant isn’t just about reliability — it’s also about food safety, hygiene, and regulatory compliance. With tight production windows and strict sanitation requirements, even small scheduling missteps can have costly consequences.
These best practices can help your team schedule smarter, reduce downtime, extend asset life, and stay inspection-ready.
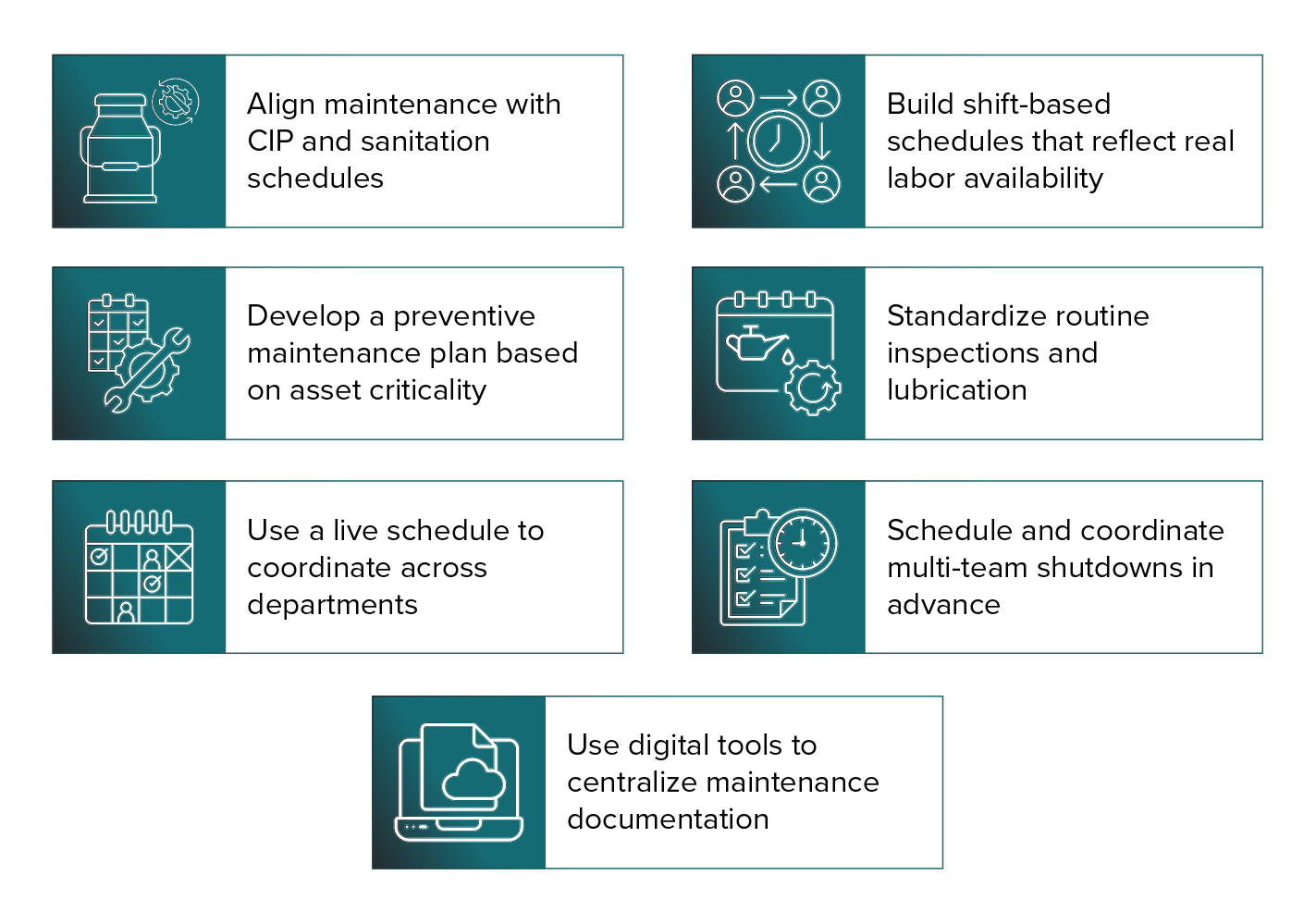
1) Align maintenance with CIP and sanitation schedules
Cleaning-in-Place (CIP) systems and sanitation routines are core to dairy plant hygiene — but they can disrupt access to equipment and throw off maintenance plans if not coordinated properly. To avoid these conflicts, maintenance should be planned in lockstep with sanitation windows.
Start by maintaining a shared schedule of all CIP cycles and cleaning tasks. This lets planners avoid booking PMs during blocked time and instead focus on windows where equipment is clean and accessible. When possible, layer in minor PMs or inspections immediately after cleaning is complete. For example:
- Schedule post-CIP tasks like gasket checks or visual inspections while equipment is still offline.
- Use color-coded calendars to distinguish cleaning from maintenance windows and prevent overlap.
- Coordinate with sanitation leads weekly to ensure plans are aligned and won’t cause rework or delays.
This level of coordination helps reduce downtime and avoid rescheduling.
2) Build shift-based schedules that reflect real labor availability
Dairy plants often run rotating shifts or mixed-coverage schedules — and maintenance needs to fit that reality. Planning PMs based only on the clock, not the crew, leads to overload on some shifts and underutilization of others.
Instead, align your maintenance schedule with how your teams actually operate. That means:
- Mapping out technician availability per shift and factoring in vacations, cross-training, and call-outs.
- Avoiding critical work on under-staffed shifts — even if a timeslot looks free, execution will suffer if key skills are missing.
- Using tools that reflect real crew capacity, like visual planners or scheduling software that surfaces labor gaps.
When the schedule reflects how the plant really runs, your team can execute more work — with fewer surprises and less burnout.
3) Develop a preventive maintenance plan based on asset criticality
Not every piece of equipment needs the same maintenance intensity. Some failures might mean a five-minute fix — others could mean spoiled product, regulatory violations, or full production halts. That’s why your PM plan should be grounded in asset criticality, not just manufacturer recommendations.
To start, assess each asset’s importance based on three factors:
- Production impact: How much would failure disrupt output or flow?
- Food safety risk: Could failure lead to contamination or non-compliance?
- Failure frequency: Is the asset known to wear out quickly or unpredictably?
Use this information to build a tiered PM program where critical equipment gets more frequent, detailed attention, while lower-risk assets are checked less often. Revisit this ranking regularly — especially after product changes or new regulatory updates. Hygiene-sensitive and important but failure-prone assets will usually be high on that list.
4) Standardize routine inspections and lubrication
Small, repetitive tasks like lubrication, motor temperature checks, and visual inspections often get overlooked — yet these tasks are crucial in preventing early wear and unexpected failures. Standardizing these routines adds a layer of reliability to your plant operations.
Rather than relying on memory or scattered notes, create consistent task lists that can be assigned to specific roles or shifts. For example:
- Build preventive maintenance checklists for different asset groups — mixers, conveyors, pumps, etc.
- Assign inspection routes based on zones so that techs develop familiarity and consistency.
- Make lubrication intervals visible at the asset, using tags or digital reminders, to reinforce routines.
These habits ensure routine care happens consistently, even in busy or short-staffed conditions.
5) Use a live schedule to coordinate across departments
In most wineries, maintenance competes with cellar work, production demands, lab tests, and deliveries — all in shared spaces. A bottling room might be in use for production all day, but is needed for equipment repairs overnight. Without visibility into each team’s plans, conflicts are inevitable.
A live maintenance schedule gives all departments more clarity on what’s happening, when, and where. By coordinating in advance, you reduce disruptions, avoid double-booking resources, and make sure essential maintenance gets done on time — without teams stepping on each other’s toes.
6) Schedule and coordinate multi-team shutdowns in advance
Even brief maintenance shutdowns of dairy processing equipment require tight coordination — not just within the maintenance team, but also with production, sanitation, and often QA. Without a clear, shared plan, these short windows can quickly spiral into costly delays, missed tasks, or rushed work that increases food safety risks.
To avoid that, start shutdown planning weeks in advance, especially when multiple departments or contractors are involved. A good shutdown plan should clearly outline:
- Who is responsible for each task, including internal crews and outside vendors.
- What work will be done, including priority levels and dependencies between jobs.
- When each job starts and ends, to prevent bottlenecks or labor conflicts.
- How long each task should take, including realistic buffers for cleaning or product changeovers.
Holding pre-shutdown meetings with all stakeholders helps surface potential conflicts early, while also ensuring everyone understands their role and timeline.
7) Use digital tools to centralize maintenance documentation
Auditors, inspectors, and internal quality teams all expect complete and accessible maintenance records. Relying on paper logs or scattered spreadsheets makes compliance harder and increases the risk of gaps.
Centralizing your documentation — whether through a CMMS, a scheduler like Sockeye, or a hybrid solution — makes it easier to track what’s been done, what’s in progress, and what’s overdue. It also ensures everyone is working from the same plan.
While you are at it, make delay tracking part of your workflow by:
- Logging every delayed task with a reason code (e.g., labor, parts, production).
- Reviewing delays weekly or monthly to identify trends or bottlenecks.
- Using delay insights to refine your planning, scheduling, staffing, or inventory practices.
With better visibility into what’s holding you back, you can make targeted changes to improve equipment reliability and uptime.
CMMS/EAM SCHEDULING BOLT-on
Simplify dairy plant maintenance scheduling
Tired of bouncing between your CMMS, whiteboards, and shift notes — while work is still falling behind? Sockeye is built for the pace, hygiene standards, and crew coordination challenges unique to dairy processing plants.
BOOK A DEMOStep 1
Get a Customized Demo
We start with a call from one of our product specialists to understand your specific needs. We then run a customized demo with your entire team so you can see how Sockeye makes scheduling easy.
Step 2
Start Your Risk-Free Trial
Test drive Sockeye using a file-based integration (Excel). This requires no investment or IT resources and just a few hours from the scheduler. Verify that Sockeye is right for you before you go all in.
Step 3
Get the Most out of Your Team
No more disjointed scheduling, missing data, & flying blind. Consistently build daily/weekly schedules, check the latest status, and maximize preventive maintenance by maximizing productivity.
Frequently Asked Questions
Sockeye uses two primary types of integration:
1. API-Based Integration
Sockeye uses API-based integration to adapt to every enterprise’s unique needs, providing customized read/write configurations with your maintenance and/or HR systems. This means that any last-minute changes made in your CMMS are reflected in Sockeye — and vice versa.
2. File-Based Integration
Sockeye uses an Excel template to port data between the CMMS and Sockeye — simply export your CMMS data into Sockeye’s Excel template and click ‘refresh’ to update your data. The implementation requires minimal effort and no IT resources or custom coding.
Learn more about integration types
A full production rollout with API integration takes 4 to 6 weeks, while a file-based integration can be done in under 2 weeks.
Sockeye’s experts handle most of the integration work; your IT team just needs to provide access (API endpoints or database views) and some oversight. Because Sockeye is cloud-based, there is no server to install or software to maintain on-premises — it’s all handled by our cloud infrastructure.
Yes, Sockeye offers a one-month trial using our file-based integration. You’ll get access to all of Sockeye’s features and support throughout the trial. To get started, share an Excel file of your schedule and join a 1-hour training session.
Sockeye supports read/write CMMS integration. The exact data exchanged typically includes work order details, scheduling fields, and resource info.
Configurations can be customized as read-only or selective write-back to accommodate your IT/security policies.
Work orders are updated according to your requirements. Typically, work orders are automatically updated when the scheduled work order end date has been reached. Work order updates made in your CMMS and Sockeye are automatically synchronized in both systems.
Sockeye allows you to input your technician and contractor shift patterns to track labor availability. You can easily edit labor availability for vacations, training, etc, with a couple of clicks.
Yes, Sockeye integration is customized according to your unique scheduling and IT requirements. Read/write integration, read only, write only specific fields, etc. — Sockeye is designed to meet your enterprise’s unique integration requirements.
We take data security very seriously. Sockeye is hosted on Microsoft Azure, which has industry-standard certifications (like ISO and SOC 2). Data is always encrypted, and backups are stored in a separate geographic region.
On the access side, we support role-based user permissions, SSO (Single Sign-on), and 2FA (two-factor authentication).
From Fortune 100 enterprises to single-site enterprises, Sockeye is ready, vetted, and prepared for your IT security review.
Learn more about Sockeye’s security
Schedule more work.
Get more work done.
Let us help you create a highly productive maintenance team.
BOOK A DEMO