FOOD MANUFACTURING MAINTENANCE SCHEDULING SOFTWARE
Simplify Scheduling and Ensure Uptime in Your Food Processing Plant
Create weekly and daily equipment schedules in minutes based on real-time labor availability and required skills. Coordinate crews around cleanouts and inspections, meet strict safety and compliance standards, and avoid downtime that puts product quality at risk.
Trusted by food manufacturers across North America
We built a scheduling tool so intuitive and effective that it takes just one hour to learn — and 98% of food plants that try Sockeye continue using it long-term.
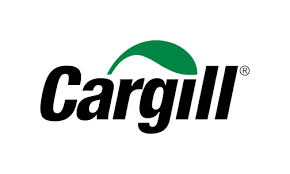
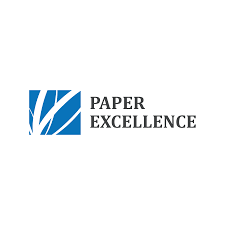
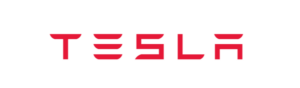
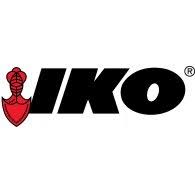
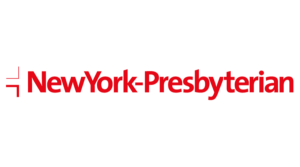
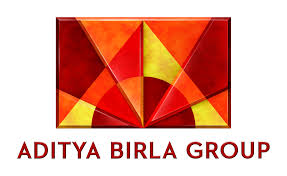
Here’s how Sockeye works
KEY FEATURES
Automatic scheduling
Schedule visualization
Work order status tracking
Delay reasons tracking
SMRP and custom KPI reports
Full CMMS/HR system integration
Perfect for
Food plants using a CMMS/EAM
Sockeye works best as a CMMS add-on. If you struggle to schedule work through existing software, use Sockeye’s intuitive interface instead.
Teams that need to do more with less
Complicated scheduling kills productivity. Our automation and availability data help you schedule more work by balancing workload between crews.
Simpler & more efficient scheduling
Sockeye is a purpose-built scheduler that’s fast to roll out, easy to use, and incredibly effective at keeping food manufacturing maintenance running smoothly.
Test Sockeye for 30 days.
No IT involvement required.
Confirm user adoption and get a proof of concept before spending a single cent.
TAKE THE FREE TRIALPM SCHEDULING
Keep up with preventive work
Sockeye’s automation makes it easy to build reliable weekly and daily schedules in just a few clicks. You can then share those live schedules to keep your team aligned and accountable.
Changes to the schedule can be done just as quickly — by simply dragging and dropping work to the next available slot.
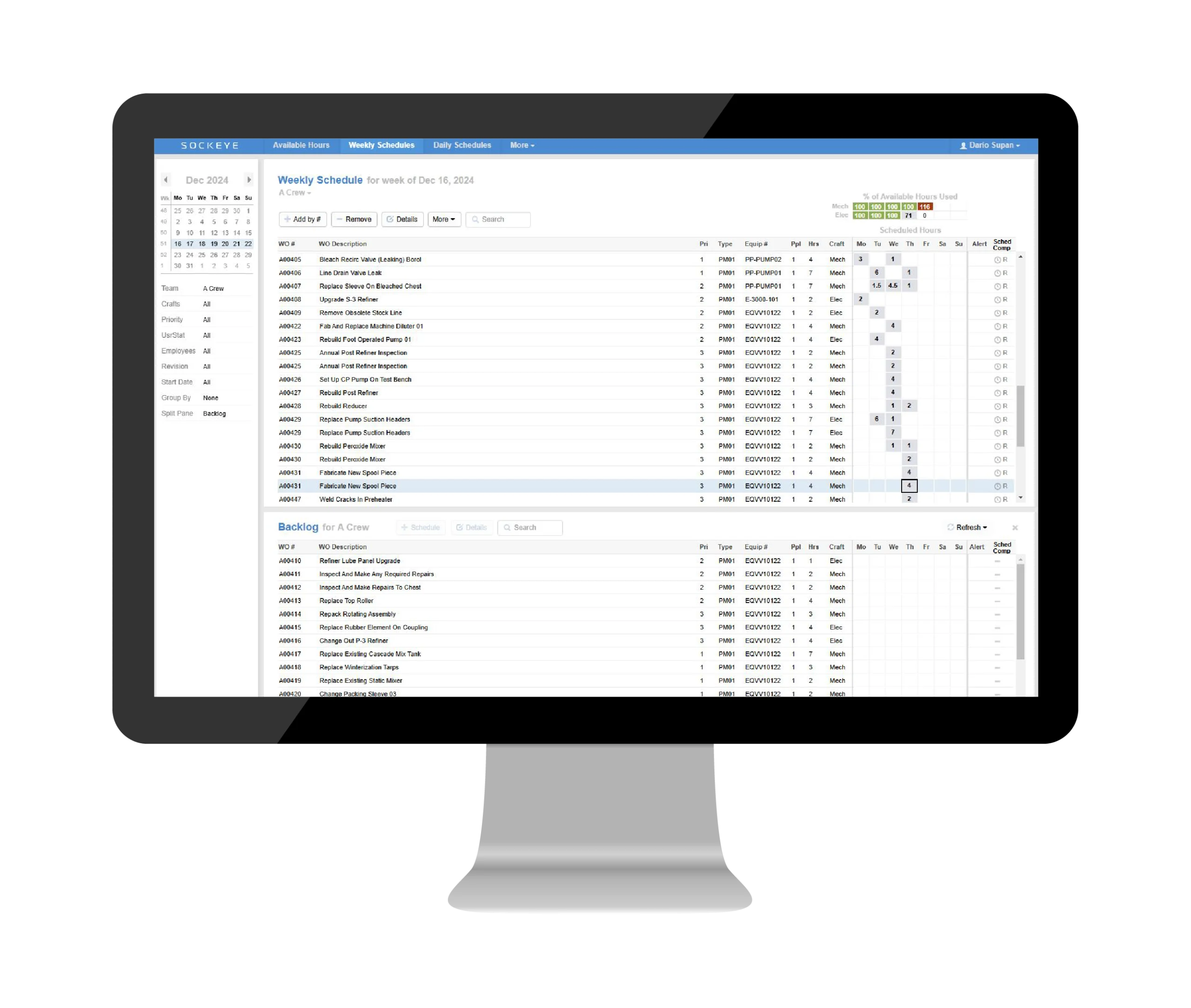
LABOR AVAILABILITY
Do more with the resource you have
Real-time visibility into crew and contractor availability helps you balance work evenly across teams and shifts, minimize scheduling conflicts, and reduce overtime.
“Sockeye identifies where deficiencies are in your man hours. For instance, if Crew A is 40 hours over schedule, but Crew B is only 35% scheduled, you can move your resources to level it out to avoid overtime pay. That saves you money.”
Todd Hicks, Planning and Shutdown Superintendent at the AV Group
EQUIPMENT RELIABILITY
Reduce downtime and extend equipment life
Unplanned downtime in food production leads to lost batches, contamination risk, and missed shipping deadlines.
Sockeye helps you prioritize preventive tasks and track why work gets delayed. This helps you uncover reliability issues early, giving your planners and schedulers more time to prepare high-quality jobs and effective schedules.
KPI REPORTING
Track and report relevant KPIs
Automatically generate SMRP and custom KPI reports for key metrics like schedule compliance, labor utilization, time spent on reactive vs preventive work, and backlog trends — then freely feed that data into your BI tools.
Track how specific work orders impact reliability and get a clear picture of the effectiveness of your current maintenance schedule.
REGULATORY COMPLIANCE
Stay audit-ready with a documented schedule
Whether it’s FDA, USDA, or SQF, Sockeye makes it easier to stay compliant. Build schedules your team can follow, document everything digitally, and always know what’s been done, what’s in progress, and what’s due next — all in one place.
Schedule more work.
Get more work done.
Let us help you create a highly productive maintenance team.
Book a DemoFood processing plant maintenance best practices
In food manufacturing, equipment issues don’t just slow production — they risk contamination, regulatory violations, and costly product loss. The best practices below are designed to help your maintenance team work smarter within tight windows, coordinate with sanitation and production, and stay ahead of breakdowns without falling behind on compliance.
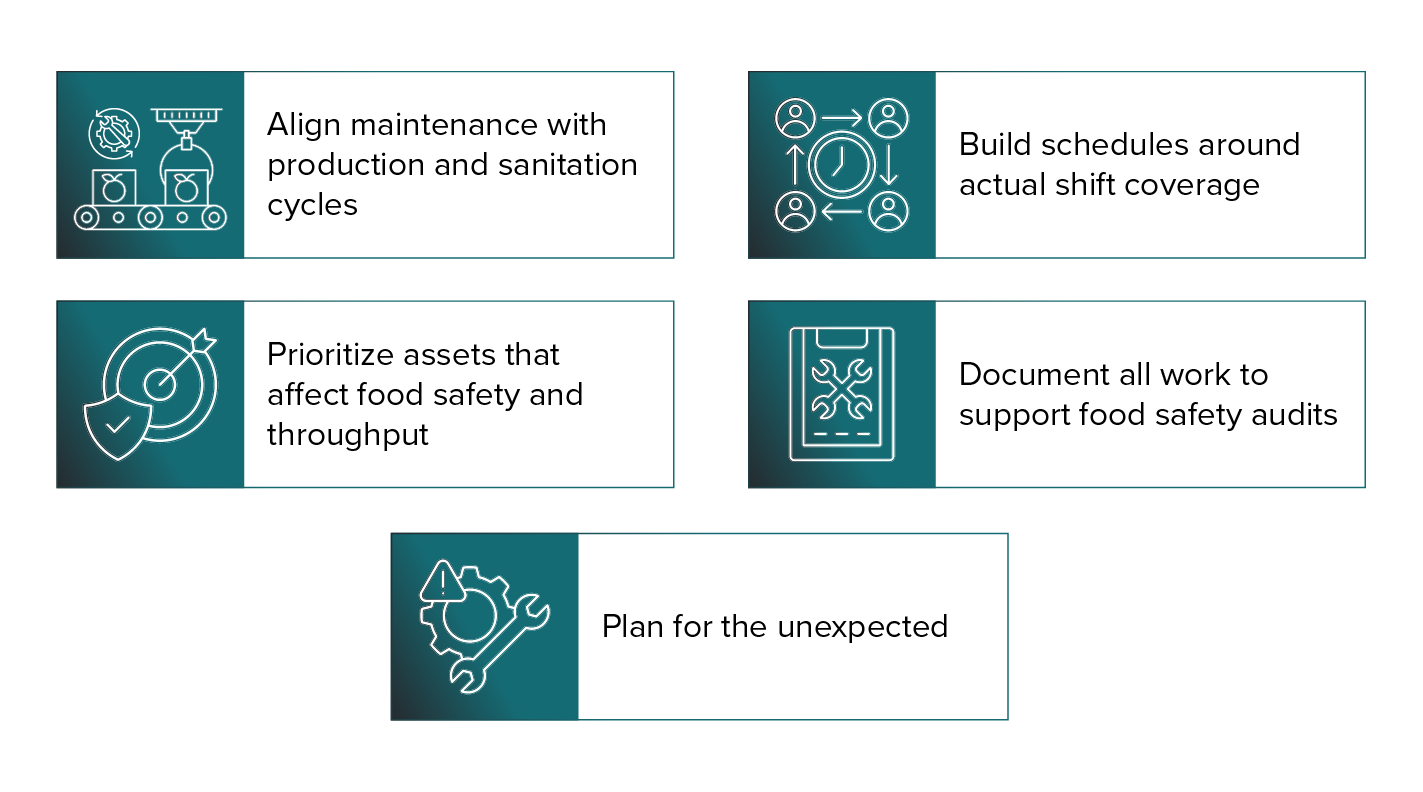
1) Align maintenance with production and sanitation cycles
Food plants run on tight, interlocking schedules — production, cleaning, and maintenance all have to happen in narrow windows. That means your schedule needs to be built around those fixed events, not in isolation.
To stay efficient, coordinate closely with production and sanitation teams to identify opportunities for shared downtime. Some planners and schedulers will map out weekly downtime opportunities in advance (e.g. shift changes, changeovers, washdowns).
They use that info to plan preventive work during natural breaks and bundle similar tasks by zone or equipment type to reduce setup/cleanup time, ensure smooth handoffs, and minimize disruptions.
For all of this to work, you will want to have a live maintenance calendar that can be shared with both production and sanitation teams.
2) Build schedules around actual shift coverage
Most food plants run 2–3 shifts per day, with varying crew capacity. Without clear visibility into crew schedules, it’s easy to overload some teams while others sit idle.
Sockeye makes it simple to build maintenance schedules around actual shift patterns and assign work that matches available skill sets on each shift. Some teams also like to rotate PM tasks across shifts so that no one team is stuck with all the cleanups or difficult jobs.
Properly leveling the workload between crews reduces overtime, prevents burnout, and enables you to accomplish more with the limited resources you have.
3) Prioritize assets that affect food safety and throughput
Not all equipment carries the same risk. A minor conveyor belt issue is inconvenient — but a failure in a refrigeration system, CIP unit, or sealer could trigger a recall.
Start by identifying high-priority assets — those most critical to uptime and compliance. Use your maintenance schedule to ensure these assets (e.g. mixers, pumps, chillers) receive consistent preventive care. For equipment with sensors or condition-monitoring, integrate that data to prioritize work based on equipment condition.
4) Document all work to support food safety audits
If your records are incomplete, missing, or inconsistent, even well-performed maintenance may be considered non-compliant.
To stay audit-ready, standardize how work is logged. Use consistent formats for PMs, corrective tasks, and inspections so that records are easy to review. Furthermore, make documentation part of the workflow. Techs should leave notes and mark completed work orders immediately upon completion — not days later.
To simplify tracking, digital tools like Sockeye will automatically log all of your preventive and reactive work in one place — creating a complete digital trail that’s audit-ready at any moment.
5) Plan for the unexpected
No schedule survives contact with reality. Equipment fails. A QC hold turns into an emergency. Sanitation takes longer than expected. Your schedule needs built-in flexibility to adjust without causing a chain reaction of delays.
What to do:
- Leave buffer slots in your weekly schedule for corrective work.
- Flag critical PMs so they’re never skipped — only rescheduled.
- Prioritize daily standups to re-align teams when things shift.
- Log delay reasons for each deferred job to learn and improve over time.
On top of everything mentioned, you will want to use a scheduling tool that makes it easy to move work to another time or crew. The goal isn’t to eliminate all surprises — it’s to build a system that can handle them without compromising food safety or uptime.
CMMS/EAM SCHEDULING BOLT-on
Simplify food plant maintenance scheduling
Juggling your CMMS, spreadsheets, and shift notes — and still missing critical PMs? Sockeye is purpose-built to handle the fast pace and complexity of food manufacturing operations.
BOOK A DEMOStep 1
Get a Customized Demo
We start with a call from one of our product specialists to understand your specific needs. We then run a customized demo with your entire team so you can see how Sockeye makes scheduling easy.
Step 2
Start Your Risk-Free Trial
Test drive Sockeye using a file-based integration (Excel). This requires no investment or IT resources and just a few hours from the scheduler. Verify that Sockeye is right for you before you go all in.
Step 3
Get the Most out of Your Team
No more disjointed scheduling, missing data, & flying blind. Consistently build daily/weekly schedules, check the latest status, and maximize preventive maintenance by maximizing productivity.
Frequently Asked Questions
Sockeye uses two primary types of integration:
1. API-Based Integration
Sockeye uses API-based integration to adapt to every enterprise’s unique needs, providing customized read/write configurations with your maintenance and/or HR systems. This means that any last-minute changes made in your CMMS are reflected in Sockeye — and vice versa.
2. File-Based Integration
Sockeye uses an Excel template to port data between the CMMS and Sockeye — simply export your CMMS data into Sockeye’s Excel template and click ‘refresh’ to update your data. The implementation requires minimal effort and no IT resources or custom coding.
Learn more about integration types
A full production rollout with API integration takes 4 to 6 weeks, while a file-based integration can be done in under 2 weeks.
Sockeye’s experts handle most of the integration work; your IT team just needs to provide access (API endpoints or database views) and some oversight. Because Sockeye is cloud-based, there is no server to install or software to maintain on-premises — it’s all handled by our cloud infrastructure.
Yes, Sockeye offers a one-month trial using our file-based integration. You’ll get access to all of Sockeye’s features and support throughout the trial. To get started, share an Excel file of your schedule and join a 1-hour training session.
Sockeye supports read/write CMMS integration. The exact data exchanged typically includes work order details, scheduling fields, and resource info.
Configurations can be customized as read-only or selective write-back to accommodate your IT/security policies.
Work orders are updated according to your requirements. Typically, work orders are automatically updated when the scheduled work order end date has been reached. Work order updates made in your CMMS and Sockeye are automatically synchronized in both systems.
Sockeye allows you to input your technician and contractor shift patterns to track labor availability. You can easily edit labor availability for vacations, training, etc, with a couple of clicks.
Yes, Sockeye integration is customized according to your unique scheduling and IT requirements. Read/write integration, read only, write only specific fields, etc. — Sockeye is designed to meet your enterprise’s unique integration requirements.
We take data security very seriously. Sockeye is hosted on Microsoft Azure, which has industry-standard certifications (like ISO and SOC 2). Data is always encrypted, and backups are stored in a separate geographic region.
On the access side, we support role-based user permissions, SSO (Single Sign-on), and 2FA (two-factor authentication).
From Fortune 100 enterprises to single-site enterprises, Sockeye is ready, vetted, and prepared for your IT security review.
Learn more about Sockeye’s security
Schedule more work.
Get more work done.
Let us help you create a highly productive maintenance team.
BOOK A DEMO