PULP AND PAPER MILL MAINTENANCE SCHEDULING SOFTWARE
Simplify Scheduling and Boost Reliability at Your Paper Mill
Stick to weekly schedules that improve equipment reliability, minimize downtime, and ensure compliance. Use Sockeye’s automation to create schedules in a couple of clicks, coordinate your crews efficiently, and stay ahead of failures in high-demand mill environments.
Used by pulp and paper mills around the world
We created a scheduling software so simple and effective that it only takes one hour to learn — and 98% of paper mills who try it continue using it long-term.
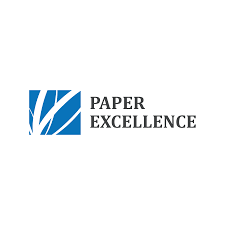
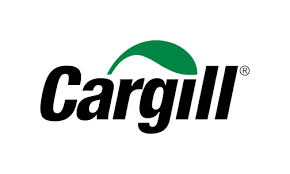
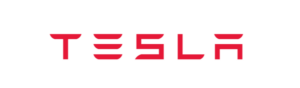
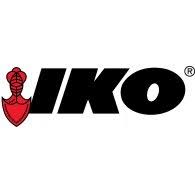
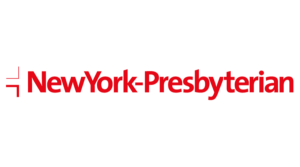
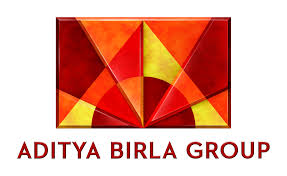
Here’s how Sockeye works
KEY FEATURES
Automatic scheduling
Schedule visualization
Work order status tracking
Delay reasons tracking
SMRP and custom KPI reports
Full CMMS/HR system integration
Perfect for
Teams that already have a CMMS/EAM
Sockeye works best as a CMMS add-on. If you struggle to schedule work through existing software, use Sockeye’s intuitive interface instead.
Teams that need to get more work done
Complicated scheduling kills productivity. Our automation and availability data help you consistently schedule more work while minimizing overtime.
Simpler & more efficient scheduling
Sockeye is a scheduler that is easy to implement and simple to use. It is solely focused on maintenance scheduling — and it is damn good at it.
Test Sockeye for 30 days.
No IT involvement required.
Confirm user adoption and get a proof of concept before spending a single cent.
TAKE THE FREE TRIALPM SCHEDULING
Simplify weekly & daily PM scheduling
Keep up with routine work like lubrication, inspections, and cleaning by building consistent weekly and daily schedules in just a few clicks.
Sockeye makes it easy to assign PMs, balance workloads, and ensure nothing gets missed — helping your team stay on track and your equipment stay reliable.
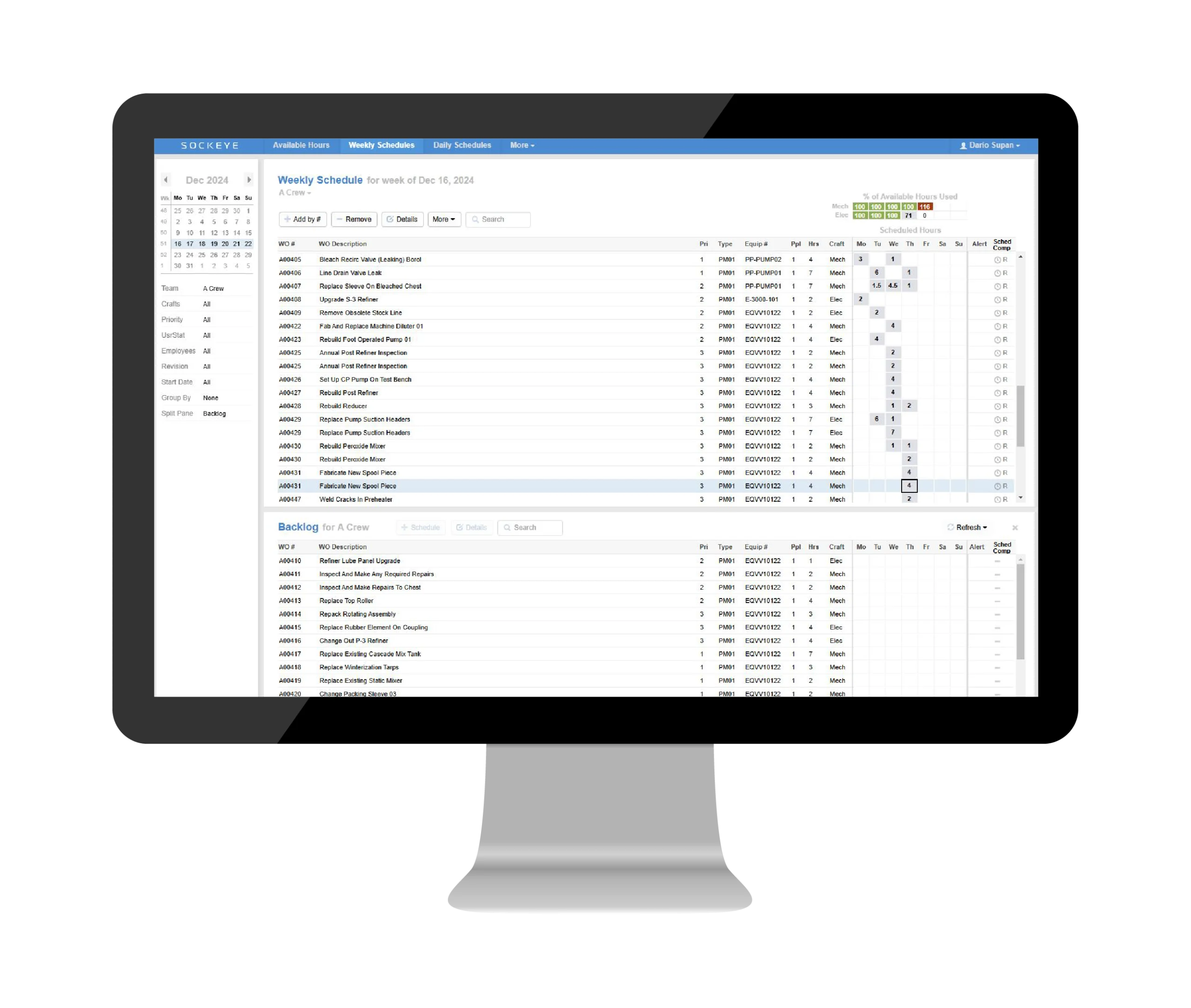
LABOR AVAILABILITY
Do more work with fewer people
Our real-time crew and contractor availability data helps you level work across teams, scheduling everyone near 100% of their capacity.
“Sockeye identifies where deficiencies are in your man hours. For instance, if Crew A is 40 hours over schedule, but Crew B is only 35% scheduled, you can move your resources to level it out to avoid overtime pay. That saves you money.”
Todd Hicks, Planning and Shutdown Superintendent at the AV Group
EQUIPMENT RELIABILITY
Improve reliability, reduce downtime
Sockeye gives your team the tools to improve reliability and cut downtime by making it easier to prioritize and schedule preventive work.
You’ll be able to track work order delay reasons to uncover recurring issues, give planners more time to prepare jobs properly, and stay on top of weekly and daily PMs.
KPI REPORTING
Track and report relevant KPIs
Automatically generate SMRP and custom KPI reports for key metrics like schedule compliance, labor utilization, time spent on reactive vs preventive work, and backlog trends — then freely feed that data into your BI tools.
Our split-pane view makes it easy to track how specific work orders impact reliability and other KPIs, giving you a clear picture of the effectiveness of your current maintenance schedule.
REGULATORY COMPLIANCE
Stay compliant with industry regulations
Regulatory compliance in pulp and paper mills depends on consistent, documented maintenance.
Sockeye’s live schedule will keep your team accountable and aligned. You’ll always know what work has been done, what’s in progress, and what’s coming up — with a digital trial for incoming audits.
Schedule more work.
Get more work done.
Let us help you create a highly productive maintenance team.
Book a DemoPulp and paper mill maintenance best practices
Keeping equipment running safely and efficiently in a pulp and paper mill requires discipline, planning, and the right tools. The following best practices will help your maintenance team stay ahead of problems, extend asset life, and reduce costly downtime.
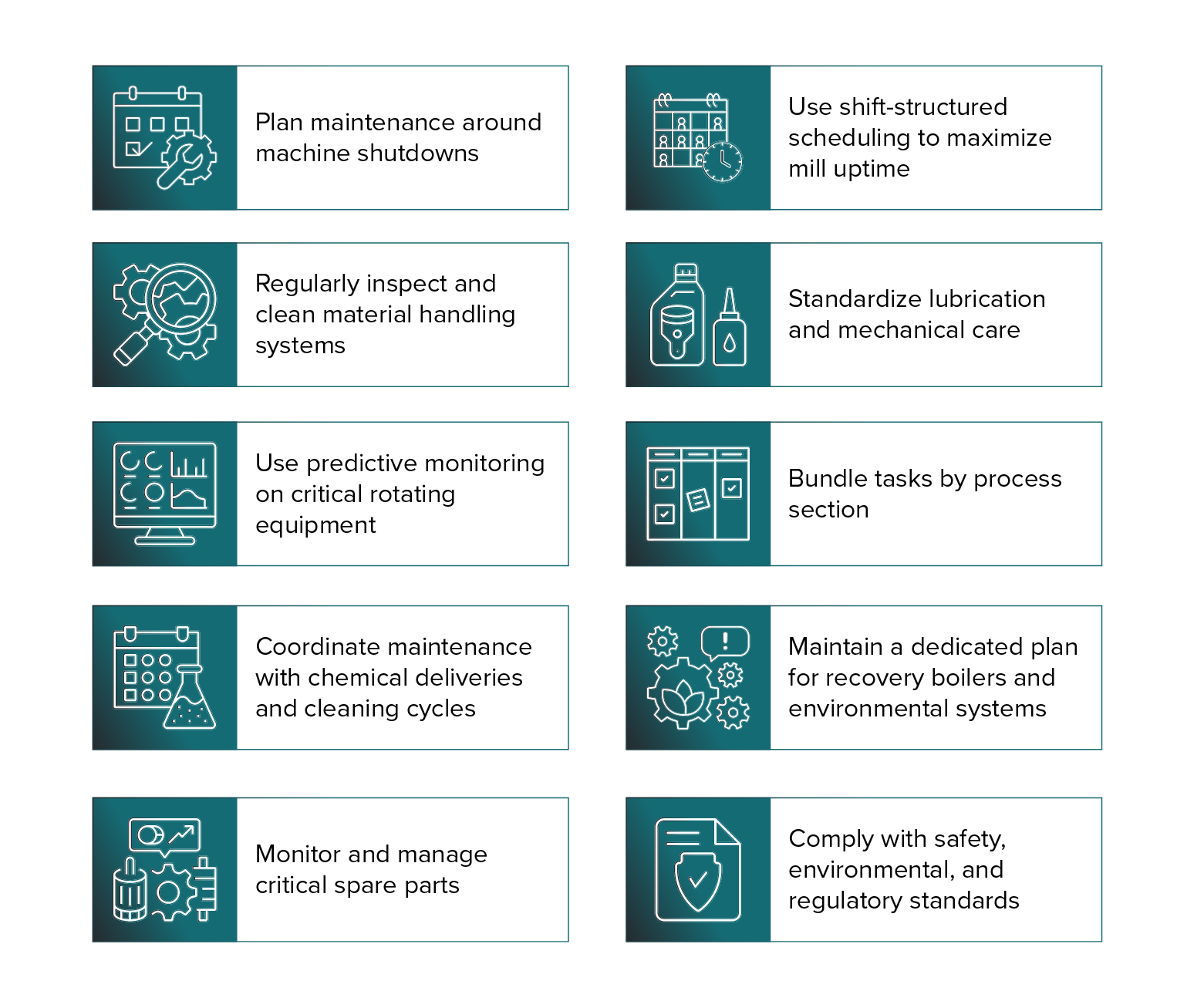
1) Plan maintenance around machine shutdowns
Paper machines typically operate non-stop for extended periods, making planned shutdowns the only opportunity to perform essential maintenance. These windows are short and high-stakes — delays or poor coordination can quickly escalate into extended downtime and production losses.
To make the most of these outages, develop detailed shutdown plans well in advance. Coordinate across departments to layer mechanical, electrical, and instrumentation work. Use scheduling software to assign tasks, allocate resources, and avoid conflicts. The more precise the plan, the more value you’ll get from each shutdown.
2) Use shift-structured scheduling to maximize mill uptime
Pulp and paper mills operate around the clock, so maintenance must fit into tight windows without disrupting production. By building your maintenance schedule around your crews’ actual shift patterns — whether it’s 12-hour rotations or alternating day/night crews — you can assign preventive work consistently and ensure coverage for critical issues.
Sockeye makes it easy to visualize shift-based availability and balance workloads between teams. This helps you avoid overloading certain crews, reduce delays, and keep essential PM tasks on track across all shifts.
3) Regularly inspect and clean material handling systems
Paper mills generate large amounts of dust, bark, wood chips, sludge, and paper waste — all of which can clog or wear down material handling systems. Equipment like chip conveyors, debarkers, bark handling systems, and reject conveyors is especially prone to buildup, abrasion, and mechanical failure.
To keep material moving efficiently through the mill, prioritize frequent inspections and lubrication of these systems. Catching buildup or wear early helps prevent blockages, reduces strain on downstream equipment, and supports consistent digester or incinerator feed rates.
4) Standardize lubrication and mechanical care
Rotating equipment in pulp and paper mills — like pumps, rolls, motors, and conveyors — is exposed to high loads, humidity, and abrasive contaminants. Without consistent lubrication and mechanical checks, premature failures are just around the corner.
To avoid that, establish a standardized lubrication schedule using the correct types and grades of lubricants for each asset. Where possible, implement automatic lubrication systems to ensure consistency. Regularly inspect belt tensions, coupling alignments, and fasteners to catch mechanical issues early.
5) Use predictive monitoring on critical rotating equipment
Vacuum pumps, refiners, dryer cans, and calendar rolls operate at high speeds under constant stress. Failures in these components can lead to sheet breaks, product defects, or even full production stoppages.
The most effective way to prevent this is to adopt condition monitoring and predictive maintenance tools — such as vibration analysis, infrared thermography, and oil analysis — to detect early warning signs of wear or imbalance.
Armed with that info, your team can plan repairs during scheduled downtime — reducing emergency breakdowns and improving machine reliability.
6) Bundle tasks by process section
Each section of the paper machine — wire, press, dryer, and reel — has its own unique maintenance needs. For example, the wire section may require fabric replacement and vacuum system checks, while the dryer section often needs steam joint maintenance and can bearing inspections.
Bundling work orders by section allows technicians to focus on one area at a time, reducing setup time, improving wrench time, and avoiding redundant shutdowns. It also simplifies planning and ensures no critical task is overlooked within each process area.
7) Coordinate maintenance with chemical deliveries and cleaning cycles
Pulp and paper processes rely heavily on chemicals for pulping, bleaching, and cleaning. Equipment like digesters, bleach towers, and washers is exposed to harsh environments and requires periodic cleaning or passivation to stay in safe operating condition.
Align maintenance activities with chemical delivery schedules, Clean-in-Place (CIP) routines, or flush cycles to minimize downtime and make efficient use of existing process interruptions. Planning around these windows lets your team perform inspections or repairs without adding extra downtime to the schedule.
8) Maintain a dedicated plan for recovery boilers and environmental systems
Recovery boilers, scrubbers, and emissions control systems are some of the most heavily regulated and maintenance-intensive assets in a pulp and paper mill. Failures in these systems can pose serious safety risks and lead to costly environmental violations.
Create dedicated preventive maintenance plans for high-risk components like smelt spouts, black liquor guns, air systems, and emissions sensors. Start by taking a look at OEM recommendations and regulatory guidelines to establish task frequency — then adjust it based on your operating conditions.
9) Monitor and manage critical spare parts
Delays in maintenance are often caused by missing or hard-to-source parts — a major risk in mills with aging equipment or long lead times. Without proper inventory planning, even routine repairs can lead to extended downtime.
Classify spare parts by criticality and lead time, and align your parts forecasting with preventive maintenance and shutdown schedules. Use barcoding or RFID to improve inventory accuracy and traceability. Keeping critical spares on hand helps ensure work gets done on time and without costly surprises.
10) Comply with safety, environmental, and regulatory standards
Pulp and paper mills must meet strict regulations around safety, emissions, and effluent discharge — missed inspections or lapses in procedure can lead to fines, incidents, or forced shutdowns.
Perform routine checks on high-risk systems like boilers, scrubbers, wastewater treatment, and fire protection. Enforce lockout/tagout (LOTO) procedures, and maintain clear records of completed work. A well-documented, compliant maintenance program protects both your workforce and your operation.
PAPER MILL MAINTENANCE
Simplify mill maintenance scheduling
Tired of jumping between your CMMS, spreadsheets, and shift notes — and still missing critical work? Sockeye is built to handle the pace, complexity, and crew coordination demands of pulp and paper operations.
BOOK A DEMOStep 1
Get a Customized Demo
We start with a call from one of our product specialists to understand your specific needs. We then run a customized demo with your entire team so you can see how Sockeye makes scheduling easy.
Step 2
Start Your Risk-Free Trial
Test drive Sockeye using a file-based integration (Excel). This requires no investment or IT resources and just a few hours from the scheduler. Verify that Sockeye is right for you before you go all in.
Step 3
Get the Most out of Your Team
No more disjointed scheduling, missing data, & flying blind. Consistently build daily/weekly schedules, check the latest status, and maximize preventive maintenance by maximizing productivity.
Frequently Asked Questions
Sockeye uses two primary types of integration:
1. API-Based Integration
Sockeye uses API-based integration to adapt to every enterprise’s unique needs, providing customized read/write configurations with your maintenance and/or HR systems. This means that any last-minute changes made in your CMMS are reflected in Sockeye — and vice versa.
2. File-Based Integration
Sockeye uses an Excel template to port data between the CMMS and Sockeye — simply export your CMMS data into Sockeye’s Excel template and click ‘refresh’ to update your data. The implementation requires minimal effort and no IT resources or custom coding.
Learn more about integration types
A full production rollout with API integration takes 4 to 6 weeks, while a file-based integration can be done in under 2 weeks.
Sockeye’s experts handle most of the integration work; your IT team just needs to provide access (API endpoints or database views) and some oversight. Because Sockeye is cloud-based, there is no server to install or software to maintain on-premises — it’s all handled by our cloud infrastructure.
Yes, Sockeye offers a one-month trial using our file-based integration. You’ll get access to all of Sockeye’s features and support throughout the trial. To get started, share an Excel file of your schedule and join a 1-hour training session.
Sockeye supports read/write CMMS integration. The exact data exchanged typically includes work order details, scheduling fields, and resource info.
Configurations can be customized as read-only or selective write-back to accommodate your IT/security policies.
Work orders are updated according to your requirements. Typically, work orders are automatically updated when the scheduled work order end date has been reached. Work order updates made in your CMMS and Sockeye are automatically synchronized in both systems.
Sockeye allows you to input your technician and contractor shift patterns to track labor availability. You can easily edit labor availability for vacations, training, etc, with a couple of clicks.
Yes, Sockeye integration is customized according to your unique scheduling and IT requirements. Read/write integration, read only, write only specific fields, etc. — Sockeye is designed to meet your enterprise’s unique integration requirements.
We take data security very seriously. Sockeye is hosted on Microsoft Azure, which has industry-standard certifications (like ISO and SOC 2). Data is always encrypted, and backups are stored in a separate geographic region.
On the access side, we support role-based user permissions, SSO (Single Sign-on), and 2FA (two-factor authentication).
From Fortune 100 enterprises to single-site enterprises, Sockeye is ready, vetted, and prepared for your IT security review.
Learn more about Sockeye’s security
Schedule more work.
Get more work done.
Let us help you create a highly productive maintenance team.
BOOK A DEMO